Le misainier grée une voile au tiers et ne possède pas de haubans. Tout au plus, les drisses peuvent être frappées sur la lisse et participer à la tenue latérale du mat.
De ce fait, le mat est soumis a des efforts de flexion importants et continus qui peuvent engendrer une fatigue et conduire à la rupture comme ici. Les défauts du bois- nœuds, collage – ne sont pas en cause. Les fibres montrent des fines traces de rupture superficielle dues vraisemblablement à un effet de fatigue du matériau.
Ce mat était constitué de deux sections 50 x 100 contrecollées en sapin blanc de pays.
Seul remède, fabriquer son semblable, si possible plus résistant.
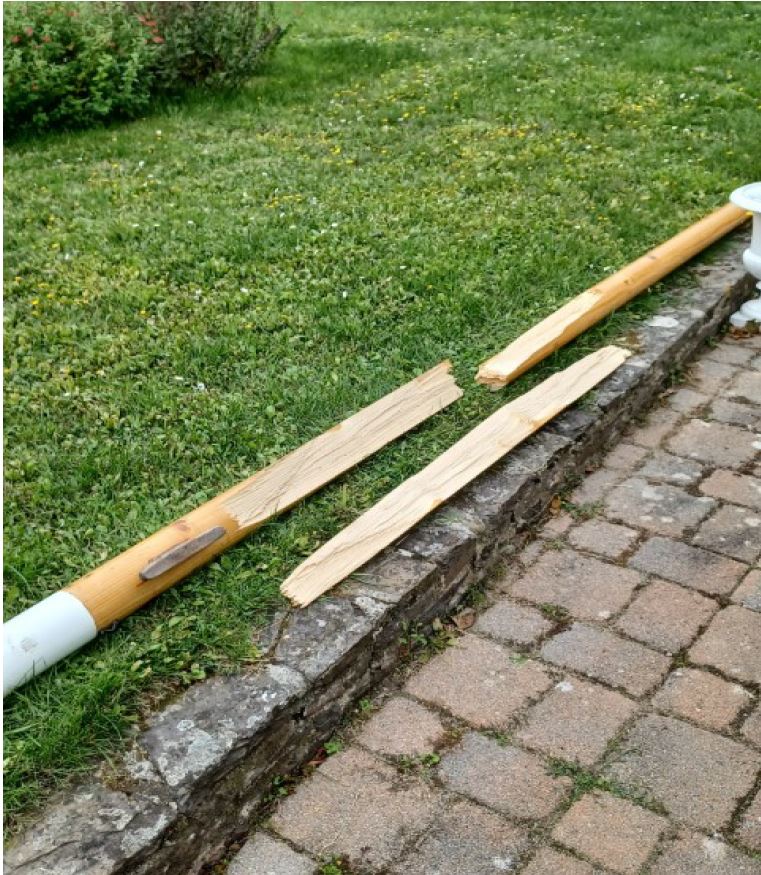
Etape 1 – recherche du bois.
Peut être la plus difficile, il faut concilier faible densité, résistance, dimensions pour faire un ensemble cohérent, séchage du matériau. L’idéal est de pouvoir choisir les pièces sur parc, ce que j’ai eu la chance de pouvoir faire.
Résultat : des planches 37×225 longueur 3,9 et 4,2m.
Le mat fini fait une section maxi de 100mm, d’ou assemblage de 3 plis, environ 34 – 32 – 34 mm avec un scarf sur la longueur pour atteindre les 6ml.
Etape 2 Préparation des plis.
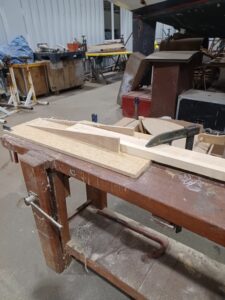
Les planches de 225 de large son débitées en 2 sur la longueur pour obtenir une section d’environ 110 de large, puis rabotées une face pour les plis extérieurs et 2 faces pour le pli intérieur de manière a disposer de plans de collage parfaitement dressés.
Les scarfs sont façonnés avec une défonceuse à l’aide d’un gabarit sommaire donnant une pente de 1/10 par passes successives
Assemblage des scarfs 2 par 2 en veillant a l’aide d’un cordeau à un parfait alignement longitudinal.
Pour les collages, j’utilise une imprégnation époxy à l’eau (Resoltech 1010) appliquée la veille du collage. Le collage peut être réalisé sans préparation supplémentaire sur cette imprégnation.
Collage sous presse avec une résine époxy classique (Resoltech 1040) . Il est utile de prévoir une butée des pièces a assembler pour éviter que les scarfs ne glissent l’un sur l’autre.
Après un délai minimum de polymérisation, nouveau passage au rabot pour bien rectifier les plans de collage sur toute la longueur.
Etape 3 – Collage
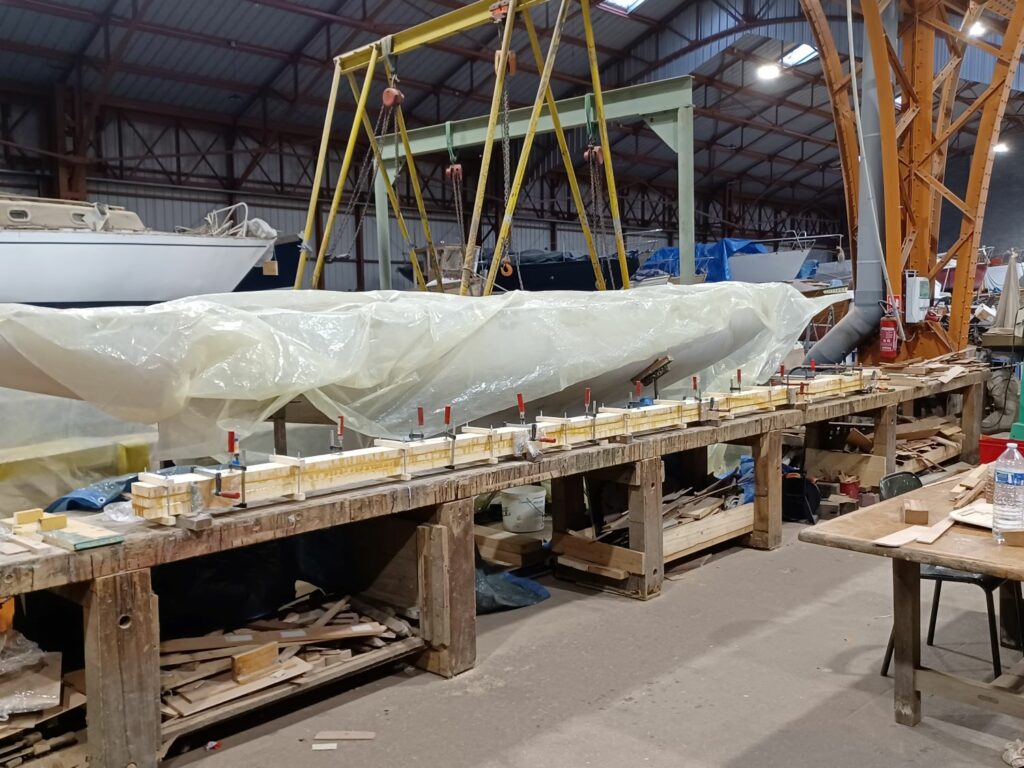
Préparation :
confection de presses avec de tasseaux 20×20 et tiges filetées,
Vérification d’une parfaite planimétrie de l’établi a mat.
Cales et serres joints.
Imprégnation époxy à l’eau, puis collages
Les presses sont disposées tous le 50cm
Des serre-joint viennent compléter l’action .
Etape 4 – Façonnage
Après un délai de polymérisation, la pièce assemblée est passée à la raboteuse pour dresser les 4 faces à la cote finale maxi de 100x100mm
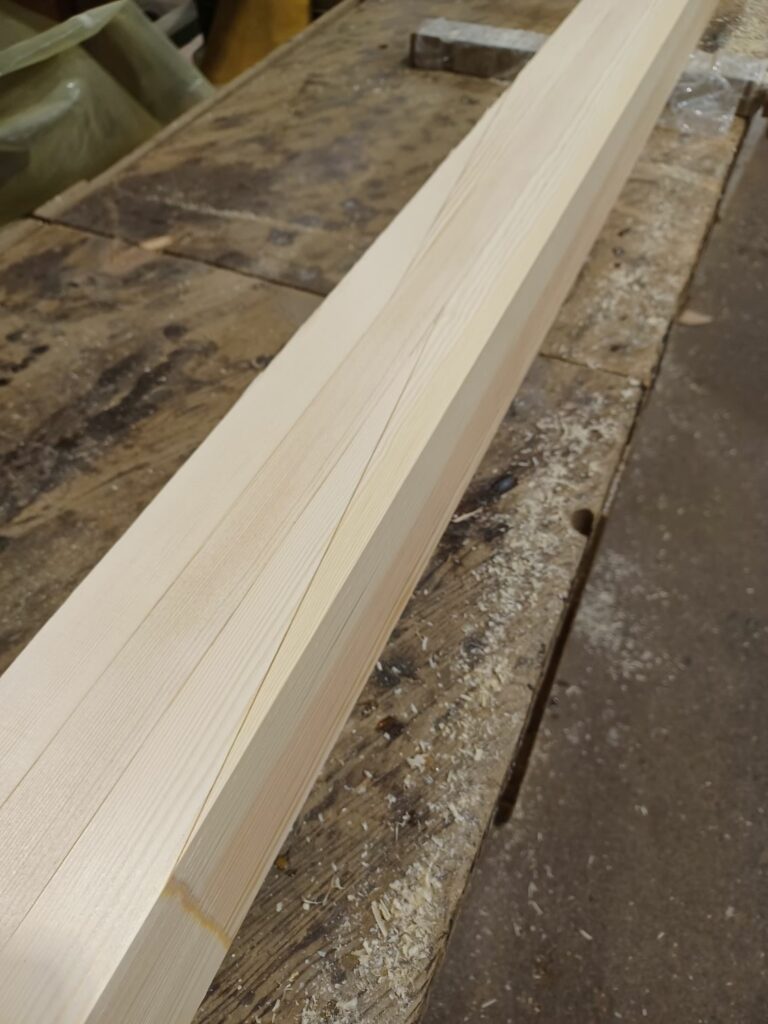
On voit ici la pièce rabotée a la cote 100×100 avec les 3 plis et un scarf sur l’un des 3 plis.
Les scarfs ont été disposés dans la partie haute du mat ou le moment de flexion est plus faible et décalés les uns par rapport aux autres. Le plus bas est le sarf central.
Partant de cette section uniforme, on trace le profil longitudinal suivant le plan du mat pour raboter manuellement (rabot électrique) de façon a amener les sections carrées à la cote finale du profil.

Après cette étape qui génère un volume certain de copeau, il est pratique de découper les cages de réa, percer les axes. Pour une meilleure tenue au frottement, la cage de réa a été découpée a une cote +10mm pour contrecoller en finition une joue en bois dur d’environ 5mm d’épaisseur de chaque coté du réa.
La méthode est simple : raboter les angles du carré pour former un octogone, continuer pour passer à l’hexadécagone (16 cotés), puis 32 avec un rabot manuel.
Finition avec une bande a poncer grain 80 de 1,20 à 1,5m de long*.
Pour guider le travail au rabot, il est utile de tracer les arêtes des polygones – Octo puis hexa – à l’aide d’un gabarit de traçage qui peut être réalisé avec une latte en bois et 2 tiges ou tubes de guidage le long de la section carrée. Un crayon placé dans les trous percés suivant les dimensions ci-contre permet de tracer les arêtes en glissant le gabarit tiges guides maintenues au contact des flans de la section carrée.
On pourra également confectionner quelques gabarits des sections intermédiaires pour contrôler la/ régularité des sections.
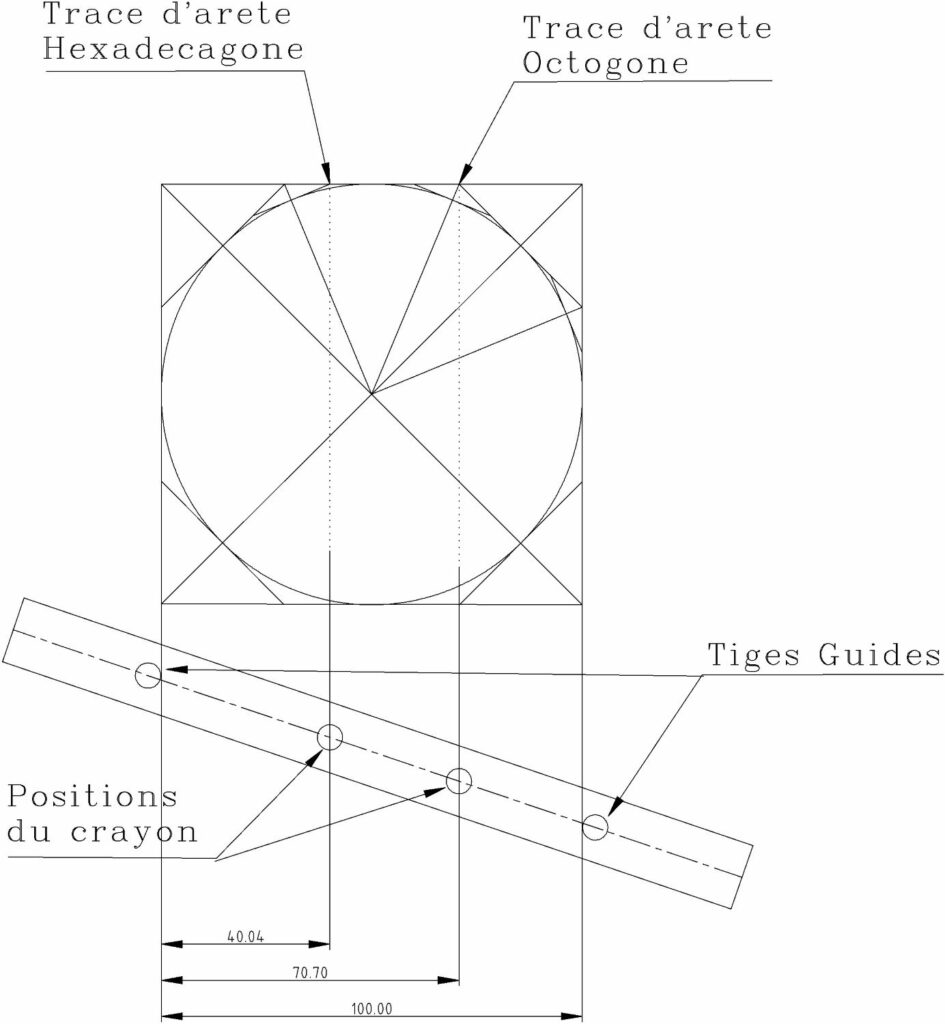
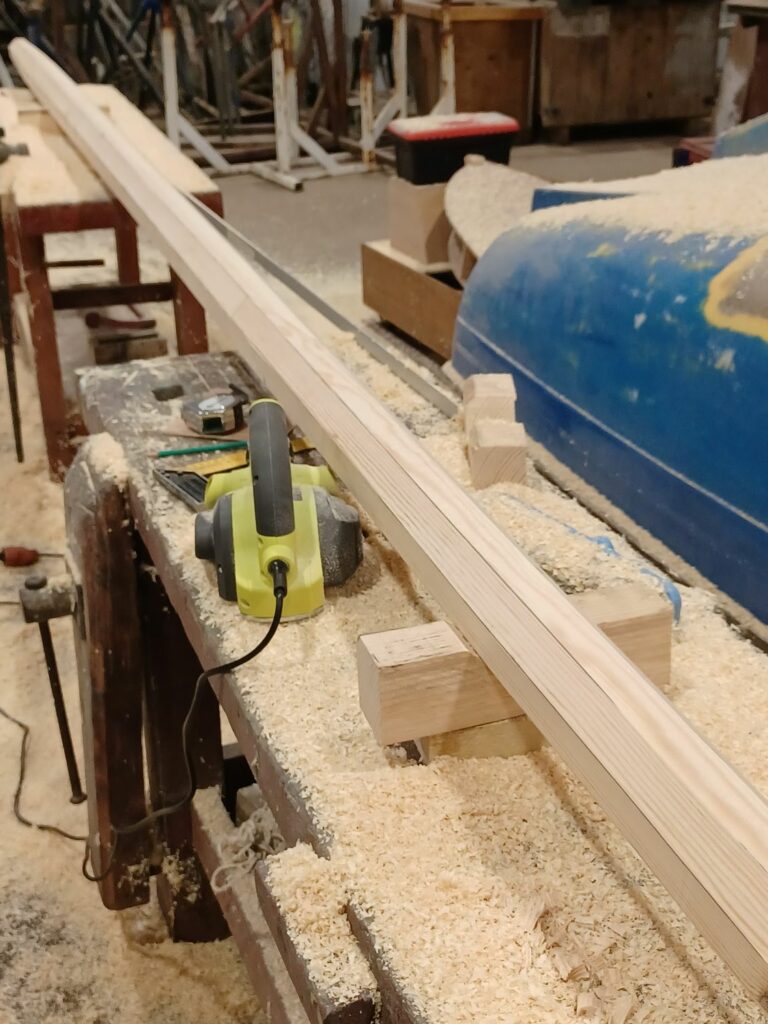
Façonnage du profil octogone
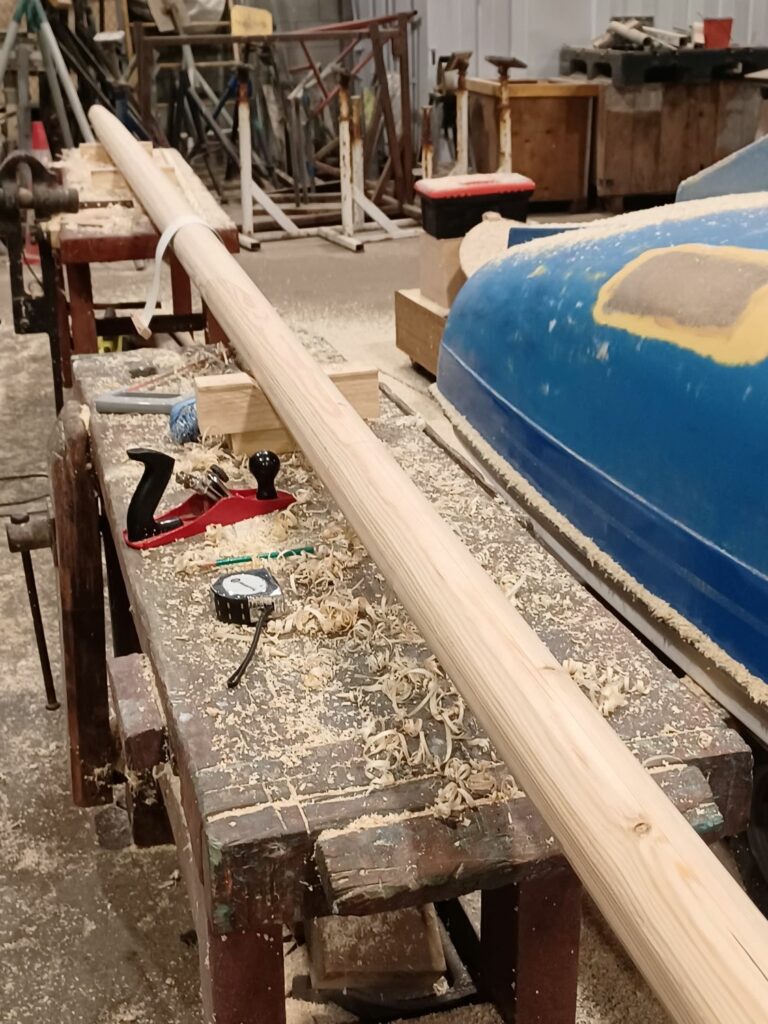
Exemple de gabarits utiles :
A – pour le traçage des arêtes octogone …
B – gabarit de largeur des différentes sections carrées pour raboter le profil en long
C – Gabarits demi-rond des différentes sections pour vérifier la mise en forme finale.
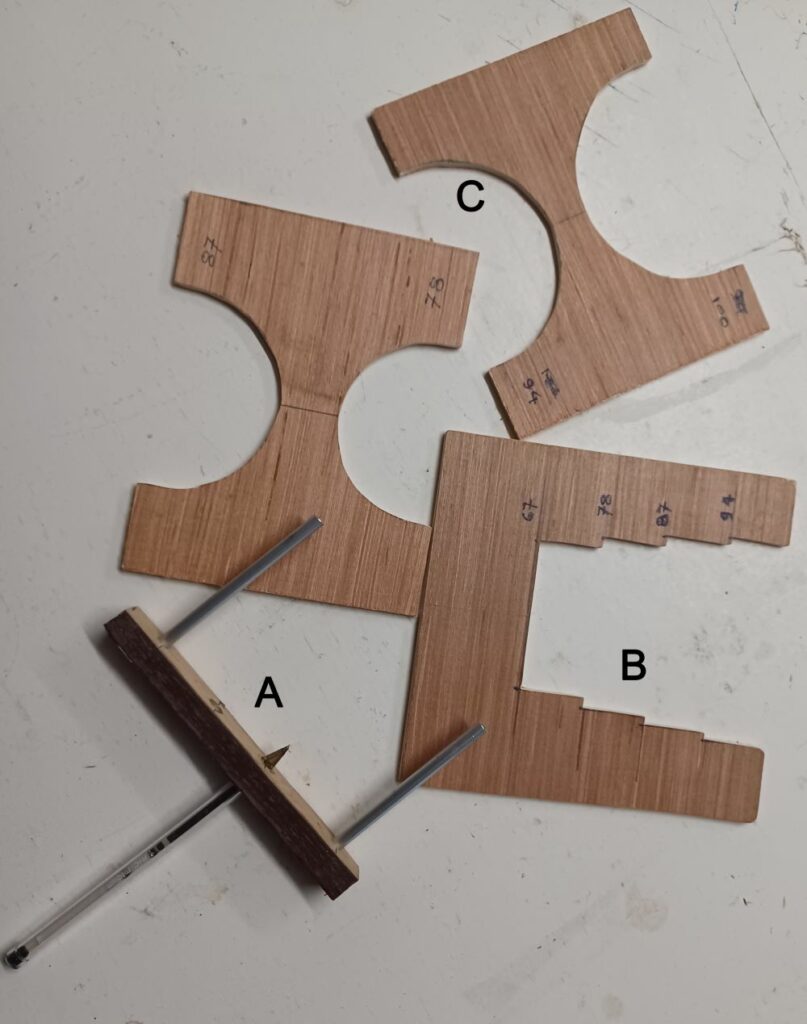
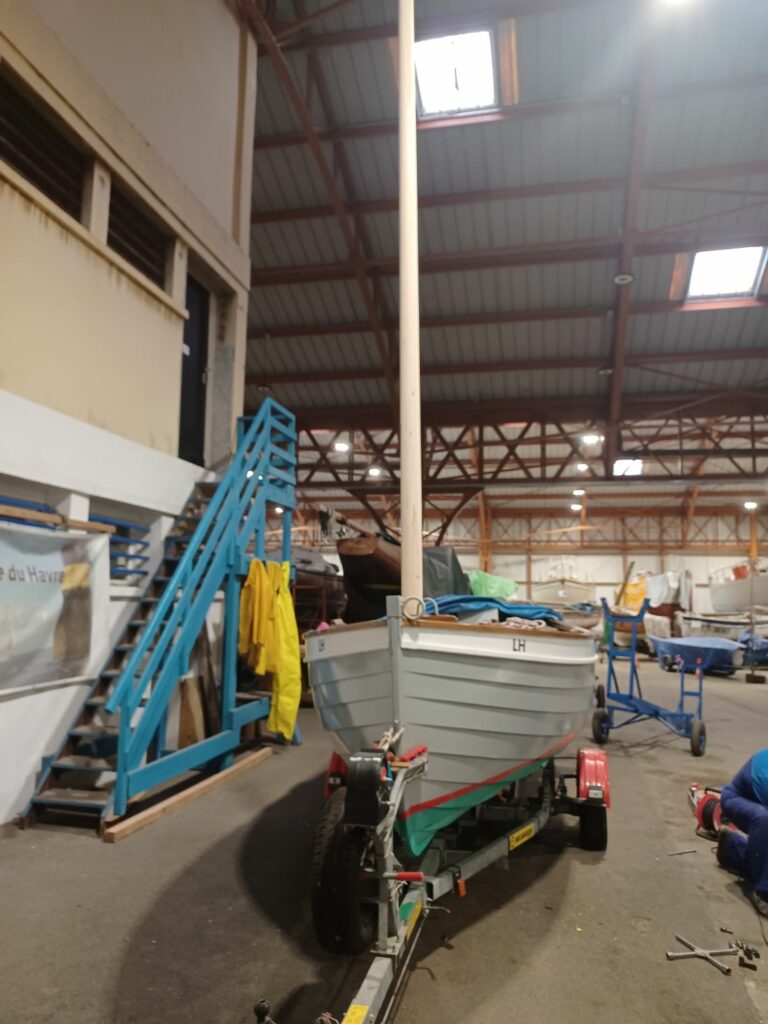
Avant finition peinture et vernis, un essai s’impose pour vérifier que tout se positionne correctement,
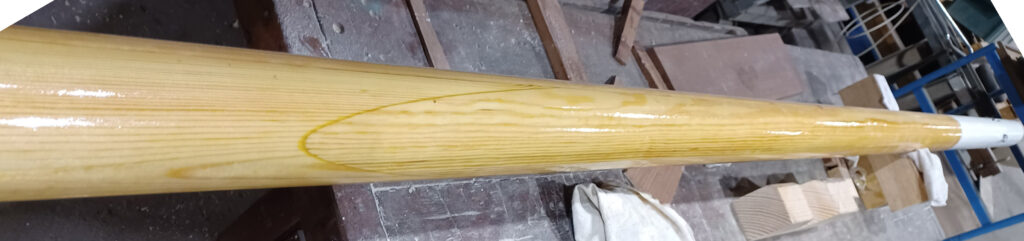